Key points
- Implementing an ergonomics program to reducing work-related musculoskeletal disorders (WMSDs).
- Implement an ergonomics program by using the top levels of the hierarchy of controls when possible.
- Administrative controls, such as job rotation and increasing breaks, can reduce WMSDs more effectively than personal protection equipment.
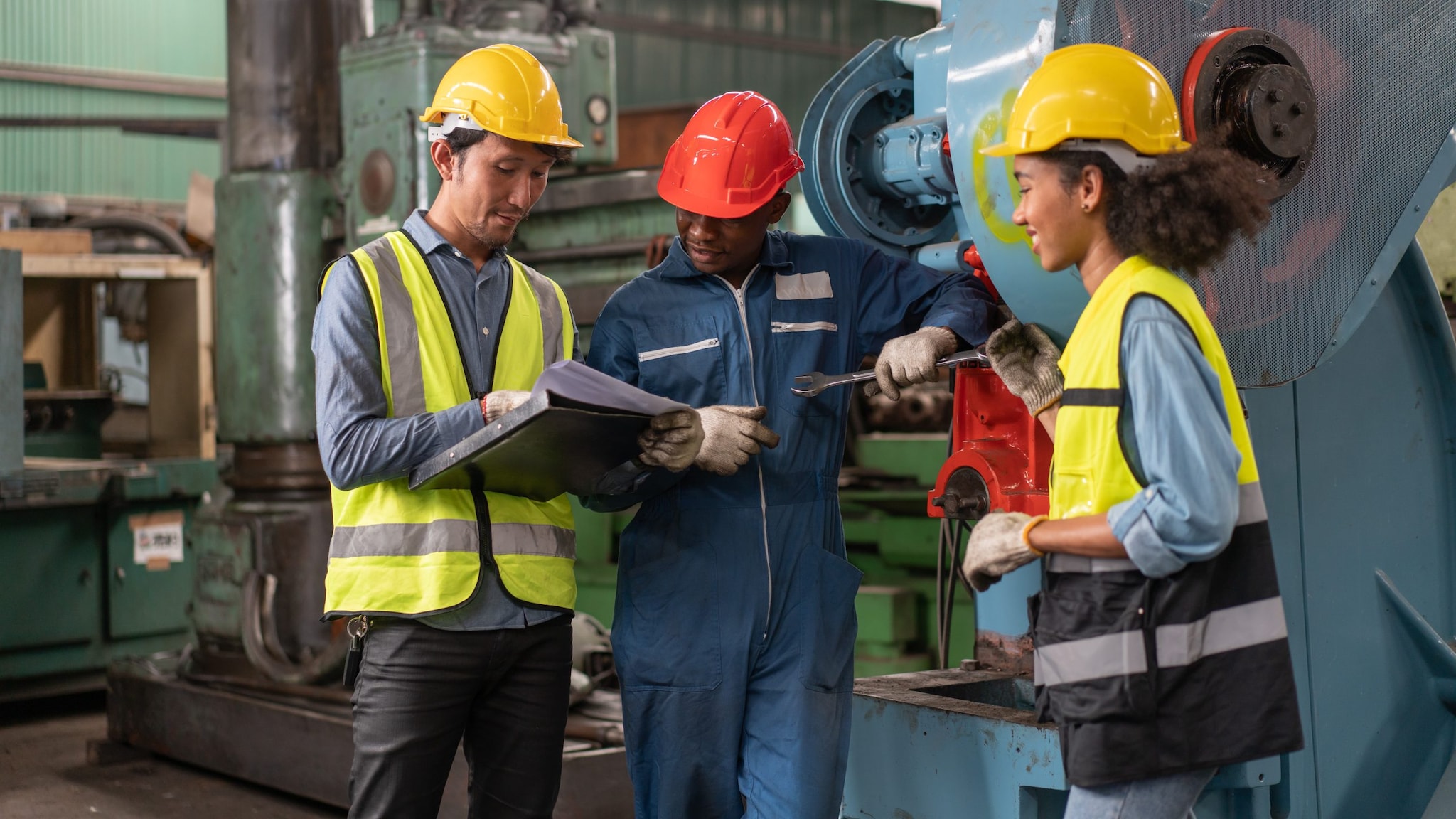
Overview
To implement an ergonomic program, begin by targeting the easiest solutions. Frequently, these will be actions you identified in your earlier analyses. This should make them some of the most effective to prevent WMSDs at your specific workplace.
Remember that early successes can build confidence in your workers and managers, while providing experience for resolving more complex WMSD problems.
Did you know?
Determine your control solution
Approaches to control WMSD risk factors fit into five categories that align with the hierarchy of controls. Elimination, or removing the hazard, is the most effective way to reduce WMSD risk factors in the workplace.
The hierarchy of controls also includes:
- Substitution (replacing the hazard).
- Engineering controls (isolating the hazard).
- Administrative controls (such as rotating tasks).
- Personal protective equipment (PPE).
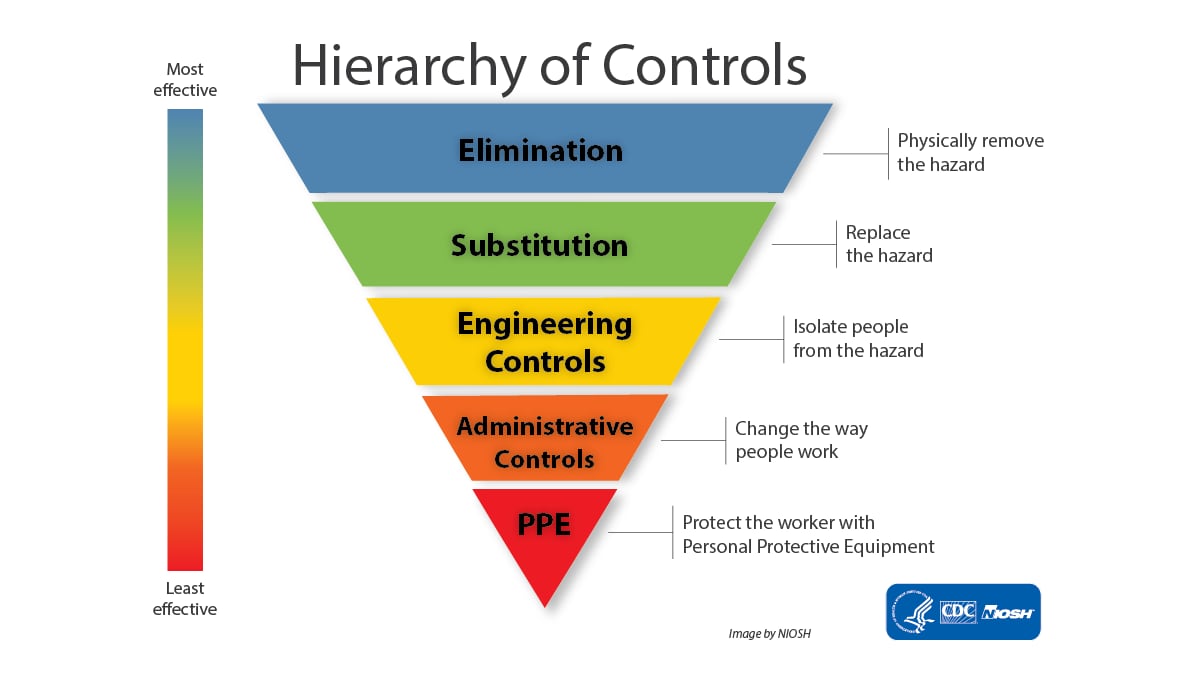
In ergonomics, the top three levels should be used before lower methods on the hierarchy. PPE and administrative controls are usually not as effective as the higher levels of the hierarchy to reduce or eliminate WMSDs.
Engineering controls are one of the most effective methods at reducing WMSD hazards. Unfortunately, they may also be the most difficult to implement for an established work process. Use engineering controls by changing the materials, parts, products, and tools workers use to relive them from WMSD risks. Implementing engineering controls can include:
- Using mechanical assist devices.
- Improving workspace lighting.
- Switching to lighter-weight packaging materials.
Administrative controls are practices and policies that workers must follow, which can make them less effective. You can use administrative controls to limit exposure to WMSD hazards by:
- Reducing the length of workers' shifts.
- Implement a job rotation.
- Schedule more breaks.
- Vary the tasks for individual jobs.
- Train employees how to minimize exposure to hazards.
Minimizing exposure to the hazard can be as simple as stepping and turning instead of twisting during manual handling.
PPE, such as knee pads, anti-vibration gloves, and grip-gloves, may protect workers from immediate hazards. PPE is inexpensive and used frequently. It can be useful where hazards cannot be reduced with engineering controls or in addition to more effective control methods. Learn more about the hierarchy of controls by visiting the NIOSH website.
Examples of interventions
To learn which intervention to use, you can find different example that may apply to your job task from several sources. Below are examples provided by the Ohio Bureau of Workers' Compensation (BWC) for construction, extended-care, manufacturing, plastics, and public industries.
- BWC Construction [PDF – 87 KB]
- BWC Extended-Care [PDF – 93 KB]
- BWC Manufacturing [PDF – 95 KB]
- BWC Plastics [PDF – 83 KB]
- BWC Public Employers [PDF – 97 KB]
Additional intervention examples
Test your intervention
You can work with many groups to come up with the right ergonomic intervention to prevent WMSD risks including:
- Trade associations.
- Workers' compensation carrier companies.
- Consultants and vendors.
- Other worksites.
Once you have a good idea, you need to test if your proposed intervention will solve your WMSD problem.
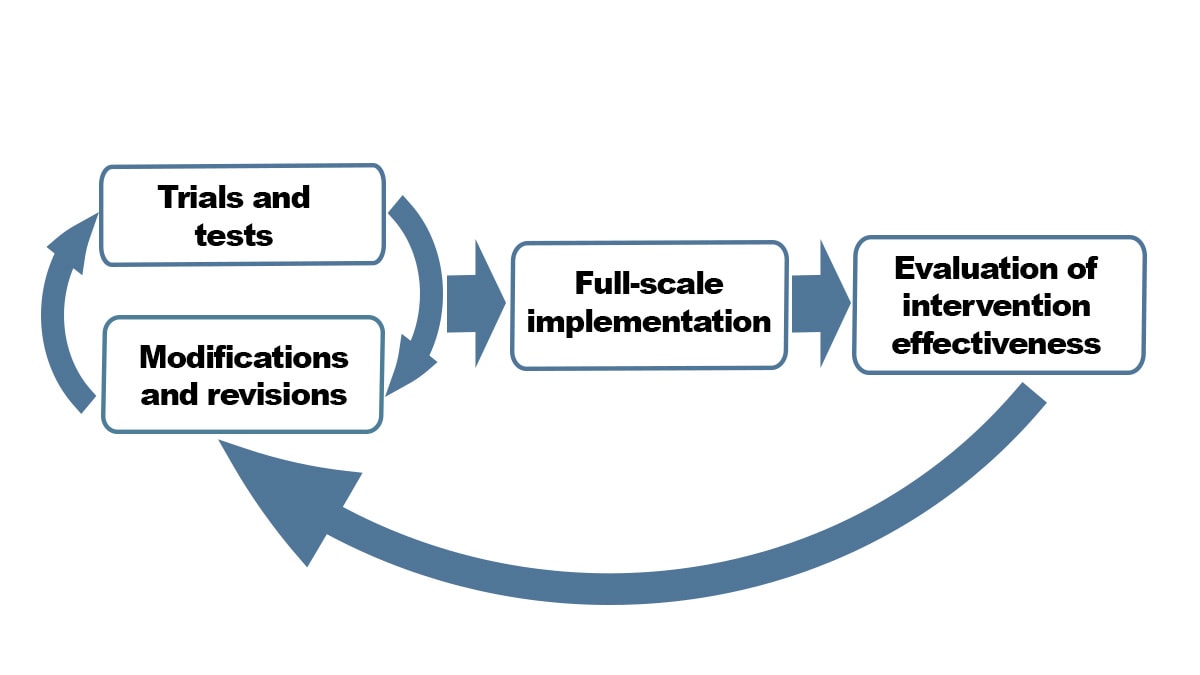
The success of an intervention depends on workers' acceptance of an idea. Try out the intervention in a limited manner and modify the proposed intervention as needed. Proceed to full-scale implementation when the pilot intervention is deemed successful.